在制造業(yè)競爭日益激烈的今天,中小企業(yè)普遍面臨三大質檢困境:人工成本攀升(單崗年成本超10萬元)、漏檢率居高不下(平均達15%導致返工損失),以及柔性不足(換產調試耗時數小時)。傳統(tǒng)依賴人眼的質檢模式,正成為制約企業(yè)提質增效的瓶頸。
一、為什么中小企業(yè)更需要2D視覺檢測?
相較于成本高昂的3D方案,成熟的2D視覺技術以更低的投入門檻和更快的回報周期,成為中小企業(yè)質量升級的首選:
降本增效:1臺標準2D檢測設備可替代6-8名質檢工,檢測速度達40片/分鐘(人工僅5片/分鐘),人力成本直降70%;
精度躍升:微米級缺陷檢出能力(如0.1mm劃痕、污漬),漏檢率<0.1%,遠超人眼極限;
柔性適配:圖形化軟件平臺支持參數化調整,新產品上線僅需更新算法模板,換型時間<1小時。
案例啟示:某電子廠手機玻璃蓋板檢測
人工暗室強光檢測時代,工人需3秒/片且漏檢率超10%;部署2D視覺系統(tǒng)后,通過明暗場融合打光技術清晰呈現玻璃表面瑕疵,AI算法自動識別百余種缺陷,檢測速度達1.5秒/片,綜合效率提升20倍。
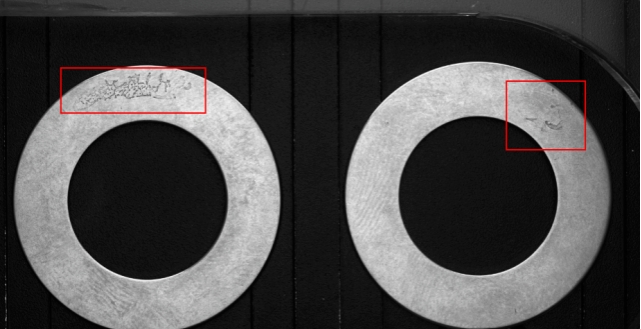
二、典型場景:中小企業(yè)的痛點破解實踐
1. 反光材質缺陷檢測(金屬件、玻璃)
痛點:強反光表面易掩蓋劃痕、凹坑,人工目檢誤差率高;
方案:采用多角度環(huán)形光源+高動態(tài)范圍成像(HDR),抑制過曝區(qū)域;融合傳統(tǒng)邊緣檢測與深度學習算法,精準分割缺陷區(qū)域;
成效:某汽車零部件廠圓柱金屬件檢測誤判率<0.1%,班產量達6000件。
2. 涂膠/密封膠條質量在線把控
痛點:膠線斷點、寬窄不一肉眼難辨,流入后道工序引發(fā)停線損失;
方案:3相機環(huán)形布局實現360°無死角覆蓋,實時測量膠條寬度、連續(xù)性(精度±0.02mm);
成效:新能源車廠涂膠質檢閉環(huán)系統(tǒng),缺陷實時報警并反饋機器人調整參數,停線率降低90%。
3. 柔性包裝與印刷品檢測
痛點:標簽錯印、包裝漏碼等缺陷波動大,傳統(tǒng)OCR誤識別率高;
方案:2D高分辨率相機+自適應定位算法,兼容尺寸/位置偏差;深度學習模型自學習新缺陷樣本,50張圖即可迭代升級23;
成效:日化企業(yè)標簽檢測線誤判率從8%降至0.3%,兼容200+產品型號自動切換。
三、技術內核:專業(yè)性與易用性的平衡
為降低中小企業(yè)應用門檻,現代2D視覺系統(tǒng)聚焦三大核心設計:
工業(yè)級可靠性:IP67防護機身抗粉塵油污,20000小時連續(xù)運行無故障;
零代碼部署:圖形化界面拖拽流程,支持PLC、機器人等10000+設備協議直連;
小樣本學習:AI算法僅需50張缺陷樣本即可訓練高精度模型,解決數據匱乏痛點。
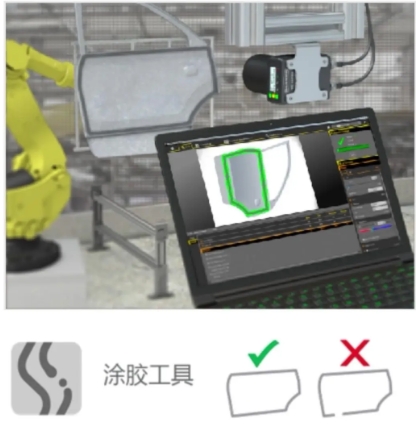
四、您的效益:可量化的升級回報
成本控制:設備投入回收周期<6個月(以替代4名質檢員計);
質量提升:客戶投訴率下降80%,品牌溢價能力增強;
產能保障:24小時連續(xù)作業(yè),交付周期縮短30%。
青島本地化服務承諾:48小時響應現場診斷 | 免費試樣檢測 | 終身軟件升級支持
立即行動,讓視覺質檢成為您的“超級質檢員”!
我們?yōu)榍鄭u設備商與集成商提供全棧式2D視覺方案——從硬件選型、算法調試到產線集成,助力您三天部署、七天投產,搶占區(qū)域智造升級先機。
工業(yè)2D視覺外觀檢測:中小企業(yè)質量升級的高效解決方案 2D視覺檢測技術——現代制造業(yè)的質量守護者