成本直降40%,效率提升300%——無(wú)需百萬(wàn)投入,2D視覺(jué)技術(shù)正重塑中小工廠品控邏輯
青島某電子元件廠曾面臨這樣的困境:每月300萬(wàn)顆微型接插件需人工目檢,20名質(zhì)檢員三班倒仍無(wú)法攔截0.3mm的引腳偏移。直到一批出口訂單因細(xì)微缺陷遭客戶索賠,損失高達(dá)季度利潤(rùn)的15%。
這樣的場(chǎng)景在中小制造企業(yè)中絕非個(gè)例。當(dāng)人力成本攀升與質(zhì)量要求嚴(yán)苛形成雙重?cái)D壓,輕量化、快部署的2D視覺(jué)識(shí)別系統(tǒng)正成為破局關(guān)鍵。
01 中小企業(yè)質(zhì)檢困局:每道傷痕都是利潤(rùn)的流失
在金屬加工車間,反光表面掩蓋的劃痕難以辨識(shí);在注塑產(chǎn)線,透明材料內(nèi)的氣泡逃過(guò)人眼捕捉;在裝配工位,錯(cuò)漏裝問(wèn)題常在交付后才暴露...這些看似微小的缺陷,正在不斷蠶食企業(yè)生存空間:
人力成本激增:某軸承企業(yè)質(zhì)檢團(tuán)隊(duì)占全員30%,年支出超200萬(wàn)
標(biāo)準(zhǔn)波動(dòng)失控:不同班次產(chǎn)品合格率波動(dòng)超15%
追溯鏈條斷裂:質(zhì)量問(wèn)題平均需4小時(shí)定位責(zé)任工序
更嚴(yán)峻的是,某包裝廠老板坦言:“90后質(zhì)檢員離職率高達(dá)80%,崗位招聘周期比設(shè)備安裝還長(zhǎng)。”
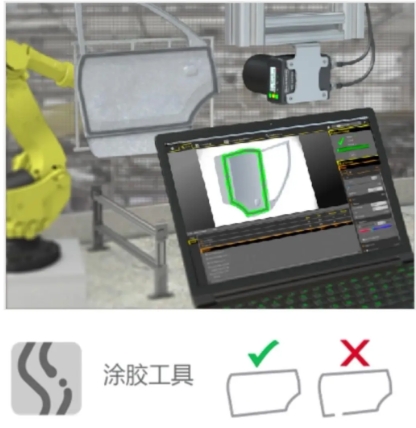
02 技術(shù)破壁:2D視覺(jué)的工業(yè)級(jí)進(jìn)化
現(xiàn)代2D視覺(jué)系統(tǒng)通過(guò)光學(xué)革新與智能算法的融合,在成本可控前提下實(shí)現(xiàn)精密檢測(cè):
成像技術(shù)突破
多光譜混合打光:消除金屬反光干擾,使0.05mm劃痕清晰可見(jiàn)
高速頻閃成像:解決傳送帶振動(dòng)導(dǎo)致的圖像模糊
智能曝光控制:適應(yīng)透明/深色材料的自動(dòng)參數(shù)調(diào)節(jié)
算法能力躍升
深度學(xué)習(xí)缺陷分類:自動(dòng)識(shí)別100+缺陷類型,誤判率<0.3%
動(dòng)態(tài)模板匹配:解決產(chǎn)品位置偏移導(dǎo)致的誤檢
數(shù)據(jù)閉環(huán)系統(tǒng):檢測(cè)結(jié)果實(shí)時(shí)反饋工藝參數(shù)優(yōu)化
青島某緊固件廠的實(shí)踐顯示:部署2D視覺(jué)后單件檢測(cè)時(shí)間從3秒壓縮至0.5秒,月度質(zhì)量成本下降37%。
03 實(shí)戰(zhàn)案例:可復(fù)制的成功范式
案例1:電子元件智能全檢
某接插件制造商部署在線檢測(cè)系統(tǒng):
同步完成引腳間距(±0.01mm)、表面瑕疵、字符印刷檢測(cè)
檢測(cè)速度達(dá)1200件/分鐘,替代16名質(zhì)檢員
通過(guò)模塊化設(shè)計(jì),產(chǎn)品換型僅需15分鐘調(diào)試
系統(tǒng)直接對(duì)接MES生成質(zhì)量云圖,使工藝缺陷定位效率提升10倍。
案例2:包裝印刷品控革命
某食品包裝企業(yè)采用移動(dòng)式檢測(cè)臺(tái):
實(shí)時(shí)監(jiān)控色差ΔE<1.5、文字漏印、套印偏差
檢出0.3mm²的污點(diǎn)與劃痕
免產(chǎn)線改造設(shè)計(jì),當(dāng)日部署即投產(chǎn)
年避免客戶索賠超180萬(wàn)元,新客戶驗(yàn)廠通過(guò)率提升至100%。
案例3:沖壓件在線分揀
汽車配件廠改造現(xiàn)有產(chǎn)線:
0.8秒內(nèi)完成孔位定位(±0.02mm)、毛刺識(shí)別、外形尺寸檢測(cè)
機(jī)械手自動(dòng)剔除不良品
系統(tǒng)自學(xué)習(xí)功能適應(yīng)模具磨損變化
使產(chǎn)品報(bào)廢率下降52%,人均產(chǎn)出提升3倍。
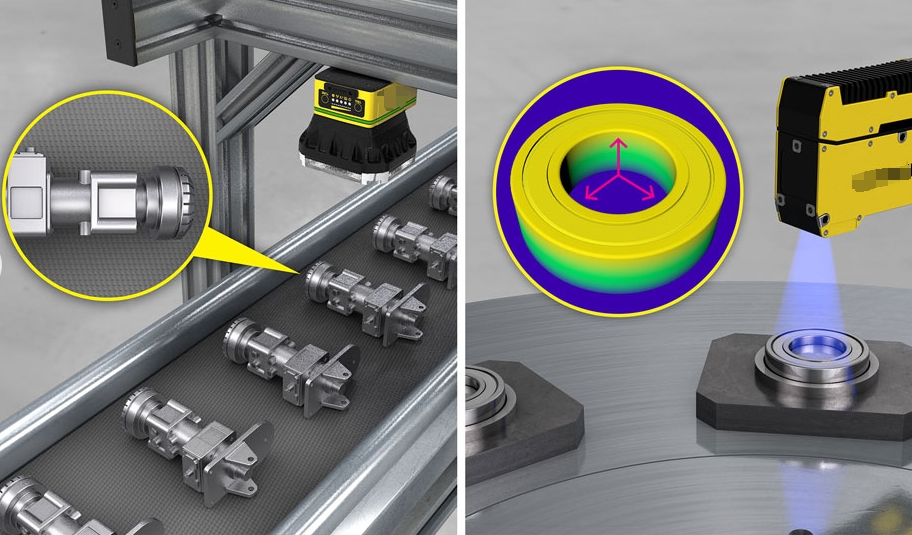
04 落地路徑:三步實(shí)現(xiàn)零風(fēng)險(xiǎn)轉(zhuǎn)型
針對(duì)中小企業(yè)痛點(diǎn)設(shè)計(jì)的漸進(jìn)式方案:
階段 | 實(shí)施重點(diǎn) | 價(jià)值錨點(diǎn)
▶ 試點(diǎn)突破 → 選擇返工率TOP2工位 → 單點(diǎn)ROI<6個(gè)月
▶ 數(shù)據(jù)積累 → 建立缺陷特征數(shù)據(jù)庫(kù) → 定位核心工藝缺陷
▶ 系統(tǒng)融合 → 對(duì)接PLC/MES系統(tǒng) → 實(shí)現(xiàn)質(zhì)量閉環(huán)控制
青島某鈑金企業(yè)僅投入12萬(wàn)元啟動(dòng)關(guān)鍵工位檢測(cè),6周后因質(zhì)量索賠減少收回成本,二期自然擴(kuò)展至全產(chǎn)線。
當(dāng)浙江某閥門廠憑借2D視覺(jué)系統(tǒng)實(shí)現(xiàn)全年零客戶退貨時(shí),生產(chǎn)總監(jiān)在晨會(huì)上宣布:“這套系統(tǒng)不是成本支出,而是我們最好的利潤(rùn)創(chuàng)造者。”
在工業(yè)檢測(cè)領(lǐng)域,精度與成本的平衡藝術(shù)正在被重新定義。青島的制造企業(yè)們發(fā)現(xiàn):那些曾屬于行業(yè)巨頭的技術(shù)紅利,如今通過(guò)輕量化2D視覺(jué)方案,正轉(zhuǎn)化為中小企業(yè)觸手可及的核心競(jìng)爭(zhēng)力。
【技術(shù)貼士】
新一代邊緣計(jì)算視覺(jué)系統(tǒng)支持:
✓ 斷電續(xù)檢:意外中斷后自動(dòng)接續(xù)檢測(cè)
✓ 自診斷功能:實(shí)時(shí)監(jiān)控相機(jī)/光源狀態(tài)
✓ 免代碼配置:圖形化界面實(shí)現(xiàn)檢測(cè)流程搭建
工業(yè)級(jí)2D視覺(jué)外觀檢測(cè):精密、高效、易部署的智能質(zhì)檢方案