在青島一家汽車零部件供應商的生產(chǎn)車間里,成箱的金屬連接件被傾倒在料框中,形態(tài)各異、堆疊交錯。過去,這里需要兩名工人不斷彎腰分揀、擺放,效率低且勞動強度大。如今,一臺搭載3D視覺的機械臂精準識別、穩(wěn)定抓取,自動將零件送入加工設備,產(chǎn)能提升40%,工人只需負責監(jiān)督與補料。
這并非大型企業(yè)的“專利”。 隨著技術(shù)成熟與成本優(yōu)化,3D視覺驅(qū)動的無序抓取解決方案正成為廣大中小型制造企業(yè)突破自動化瓶頸、提升競爭力的關(guān)鍵鑰匙。
中小企業(yè)自動化痛點:無序來料,如何應對?
物料雜亂無章: 來料(鑄件、鍛件、注塑件、袋裝物品等)常以堆疊、散亂形式出現(xiàn),傳統(tǒng)機械臂“無從下手”。
產(chǎn)線切換頻繁: 多品種、小批量生產(chǎn)成為常態(tài),固定編程的自動化設備難以適應快速換型需求。
空間與成本受限: 大型定制化方案投入高、周期長,中小廠房空間也往往捉襟見肘。
招工難、管理難: 重復性、高強度分揀崗位人員流動性大,管理成本攀升。
3D視覺無序抓取,正是為破解這些難題而生。
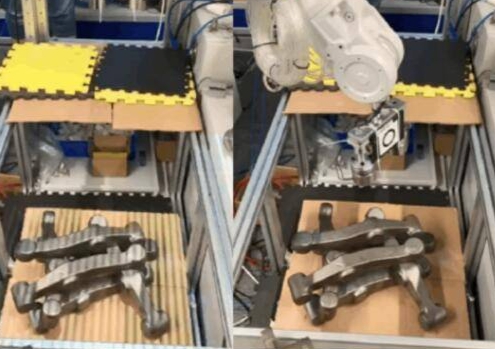
3D視覺如何“慧眼識物,巧手抓取”?
1.精準“看見”復雜世界:
超越2D局限: 普通相機只能獲取平面信息,而3D視覺通過激光或結(jié)構(gòu)光掃描,瞬間獲取物體表面數(shù)百萬個點的深度信息(點云),構(gòu)建真實三維模型。
無視光照干擾: 無論車間光線明暗變化,或是物體反光、暗色,都能穩(wěn)定成像,識別物體真實形狀和位置。
穿透雜亂堆疊: 強大的算法能有效分割相互接觸甚至部分遮擋的物體,精準定位每一個目標。
2.智能“大腦”決策規(guī)劃:
識別與定位: 基于點云數(shù)據(jù),智能算法快速識別物體類型(即使姿態(tài)萬千),并精確計算出其在空間中的位置(X, Y, Z)和姿態(tài)(旋轉(zhuǎn)角度)。
最優(yōu)路徑規(guī)劃: 系統(tǒng)自動為機械臂規(guī)劃最高效、無碰撞的抓取路徑和順序,確保動作流暢、節(jié)拍緊湊。
柔性適應變化: 更換產(chǎn)品?只需在系統(tǒng)中更新新物件的3D模型和抓取策略,無需繁瑣的硬件調(diào)整或重新編程,快速切換。
3.穩(wěn)定“執(zhí)行”可靠抓。
賦能中小企業(yè):真實場景,切實收益
案例一:青島某家電配件廠 - 注塑件無序上料
①上料節(jié)拍提升35%,注塑機利用率顯著提高。
②實現(xiàn)混線生產(chǎn),不同型號自動識別分揀,錯誤率為零。
③釋放2名工人,轉(zhuǎn)至更高價值崗位。
④投資回收期:<6個月。

案例二:山東某機械加工車間 - 鑄件毛坯抓取
①實現(xiàn)24小時無人化上料,機床利用率提升至85%以上。
②杜絕人工搬運的安全風險及毛坯碰傷。
③適應多種毛坯型號切換,生產(chǎn)柔性大幅增強。
④投資回收期:≈8個月。
為什么現(xiàn)在正是中小企業(yè)的時機?
技術(shù)成熟可靠: 核心算法(點云處理、位姿估計、運動規(guī)劃)歷經(jīng)工業(yè)場景驗證,穩(wěn)定性與精度滿足嚴苛生產(chǎn)要求。
成本持續(xù)優(yōu)化: 核心硬件(3D相機、工業(yè)計算機)成本顯著下降,方案整體性價比大幅提升,進入中小企業(yè)可承受范圍。
部署快速便捷: 模塊化設計,對現(xiàn)有生產(chǎn)線改造干擾小,通常數(shù)周內(nèi)即可完成部署調(diào)試。
投資回報明確: 如上案例所示,通常在3-9個月內(nèi)即可通過提升效率、節(jié)省人力、減少浪費收回投資。
破局無序,智贏未來
3D視覺無序抓取,已不再是遙不可及的前沿科技。它是幫助中小制造企業(yè)應對柔性生產(chǎn)挑戰(zhàn)、突破用工瓶頸、提升產(chǎn)線智能化水平的成熟、可靠、且經(jīng)濟可行的解決方案。面對散亂堆疊的物料,不再需要望“料”興嘆。
您的產(chǎn)線上,是否也存在這樣的挑戰(zhàn)?
我們扎根青島,專注為設備制造商、自動化集成商及制造企業(yè)提供前沿、穩(wěn)定、高性價比的工業(yè)3D視覺解決方案。 從精準無序抓取到高精度測量檢測,我們助力合作伙伴將先進視覺技術(shù)轉(zhuǎn)化為切實生產(chǎn)力。
讓復雜無序,歸于精準有序。讓自動化難題,迎刃而解。
您是否也期待用更智能的方式解決無序抓取難題?歡迎交流您的具體場景,獲取針對性解決方案思路。 (可聯(lián)系我們:免費初步評估/獲取行業(yè)案例集/技術(shù)白皮書等入口)