在金屬加工、3C電子、汽配鑄造等行業(yè),表面打磨一直是人力密集、環(huán)境惡劣的“硬骨頭”:人工成本高、粉塵危害大、工藝一致性差,而傳統(tǒng)自動化方案又因編程復(fù)雜、換型困難讓中小企業(yè)望而卻步。如今,“協(xié)作機器人+3D視覺+力控技術(shù)”三位一體的解決方案,正以柔性化、低門檻的優(yōu)勢,為中小企業(yè)打開自動化打磨的新大門。
一、真實痛點:中小企業(yè)打磨環(huán)節(jié)的三大困局
1.人工依賴度高
2.工藝一致性差
3.自動化改造難
二、破局案例:3D視覺如何賦能協(xié)作機器人“手眼協(xié)同”
案例1:多品種鑄鐵鍋具無人化打磨
背景:青島某外貿(mào)鍋具廠,代工10余種尺寸鍋具,人工打磨效率低且工傷頻發(fā)。
方案:
▶︎ 高精度3D視覺定位:掃描無序堆疊的鍋具,實時生成三維點云模型,識別澆口、毛刺位置;
▶︎ 免編程路徑規(guī)劃:算法自動生成最優(yōu)打磨軌跡,同步至協(xié)作機器人,換型時僅需更換軟件參數(shù);
▶︎ 力控自適應(yīng)調(diào)節(jié):機器人末端搭載力控傳感器,動態(tài)調(diào)整打磨壓力,避免過磨或漏磨。
成效:
→ 人工替代率100%,粉塵危害徹底消除;
→ 打磨合格率從82%提升至95%+,年節(jié)省返工成本50萬元;
→ 新工件導(dǎo)入調(diào)試時間從2天縮短至2小時。
案例2:筆記本合金面板全自動精磨
挑戰(zhàn):面板反光性強、尺寸精度要求±0.1mm,人工目檢易遺漏劃痕。
方案亮點:
▶︎ 抗干擾藍光成像:采用藍光結(jié)構(gòu)光3D相機,克服金屬反光干擾,定位精度達±0.05mm;
▶︎ 狹小空間適配:相機臂載式安裝于機器人末端,在機床內(nèi)部完成定位,無需改造產(chǎn)線布局。
價值:
→ 良率提升18%,年報廢損失減少200萬元;
→ 單工位節(jié)拍縮短至40秒,產(chǎn)能提升25%。
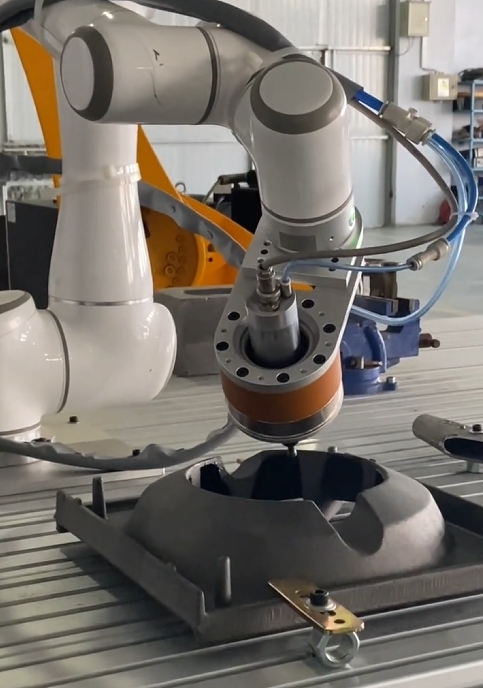
三、技術(shù)內(nèi)核:為什么中小企業(yè)現(xiàn)在能“用得起、用得好”?
1.視覺引導(dǎo):讓機器人“看得懂”
2.力控技術(shù):讓機器人“控得穩(wěn)”
3.柔性部署:低成本快速落地
四、選擇青島本土3D視覺服務(wù)商的四大理由
1.工業(yè)場景深耕:方案經(jīng)造船鋼板打磨、汽車鑄件修整等重工況驗證,魯棒性強;
2.快速響應(yīng)閉環(huán):青島及周邊區(qū)域提供48小時現(xiàn)場支持,保障產(chǎn)線“零停工”;
3.開放生態(tài)集成:支持主流協(xié)作機器人品牌(如遨博、艾利特)及PLC系統(tǒng),無縫對接現(xiàn)有設(shè)備;
4.投資回報可見:典型項目回本周期6-12個月,效率提升20%+、不良率下降15%+。
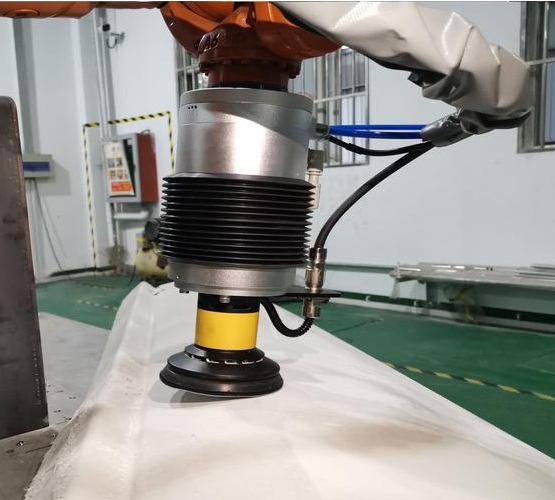
結(jié)語:打磨不再是“苦役”,而是智能升級的突破口
從鍋具、筆記本外殼到發(fā)動機缸體,3D視覺+協(xié)作機器人的組合正以柔性化、輕量化、高性價比的優(yōu)勢,成為中小企業(yè)打磨工藝升級的首選。無需推翻現(xiàn)有產(chǎn)線,無需巨額投入,即可實現(xiàn)“無人化、零缺陷”的精密打磨。
立足青島,服務(wù)智造——讓我們?yōu)槟纳a(chǎn)線裝上“慧眼”與“巧手”!
→ [獲取行業(yè)專屬方案] → [預(yù)約現(xiàn)場演示]