在工業(yè)自動(dòng)化領(lǐng)域,傳統(tǒng)生產(chǎn)模式正面臨效率瓶頸與精度挑戰(zhàn)。作為設(shè)備制造商與自動(dòng)化集成商,如何通過(guò)創(chuàng)新技術(shù)幫助客戶突破產(chǎn)線升級(jí)的困局?3D視覺(jué)引導(dǎo)技術(shù)憑借其空間感知與智能決策能力,正在成為中小型制造企業(yè)實(shí)現(xiàn)精準(zhǔn)化、柔性化生產(chǎn)的核心支撐技術(shù)。
典型應(yīng)用場(chǎng)景解析
案例一:汽車零部件高精度裝配
某北方設(shè)備制造商為汽車配件廠商開(kāi)發(fā)變速箱裝配線時(shí),面臨復(fù)雜工件姿態(tài)識(shí)別難題。通過(guò)部署3D視覺(jué)引導(dǎo)系統(tǒng),采用多角度點(diǎn)云融合技術(shù),實(shí)現(xiàn)0.05mm級(jí)定位精度。系統(tǒng)可自動(dòng)補(bǔ)償傳送帶振動(dòng)誤差,引導(dǎo)機(jī)械手完成精密軸孔裝配,使裝配合格率從82%提升至99.6%,單線產(chǎn)能提升40%。
案例二:電子元件智能檢測(cè)
某華南電子企業(yè)為微型連接器生產(chǎn)設(shè)計(jì)質(zhì)檢工站時(shí),傳統(tǒng)2D視覺(jué)無(wú)法檢測(cè)引腳空間形變。3D視覺(jué)系統(tǒng)通過(guò)條紋結(jié)構(gòu)光掃描,構(gòu)建三維尺寸模型,結(jié)合深度學(xué)習(xí)算法,可同時(shí)檢測(cè)0.1mm級(jí)高度差與平面度偏差,誤檢率降低至0.3%,檢測(cè)效率較人工提升6倍。
案例三:柔性化物流分揀
某華東物流裝備商為電商倉(cāng)儲(chǔ)改造分揀線時(shí),需處理300+SKU的混合紙箱。3D視覺(jué)系統(tǒng)通過(guò)實(shí)時(shí)體積測(cè)量與重心分析,動(dòng)態(tài)規(guī)劃?rùn)C(jī)械臂抓取路徑,兼容不同尺寸、堆疊狀態(tài)的包裹,分揀速度達(dá)1200件/小時(shí),設(shè)備投資回收周期縮短至8個(gè)月。
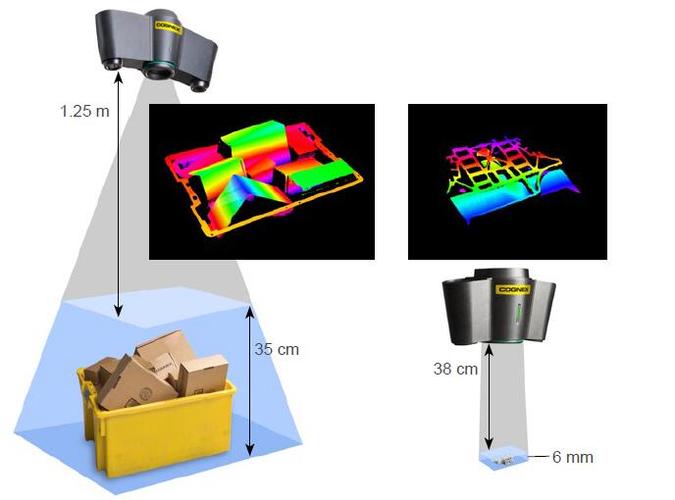
技術(shù)賦能的核心優(yōu)勢(shì)
復(fù)雜場(chǎng)景適應(yīng)能力
通過(guò)多傳感器融合與動(dòng)態(tài)標(biāo)定技術(shù),有效應(yīng)對(duì)反光、陰影、遮擋等工業(yè)現(xiàn)場(chǎng)干擾,環(huán)境適應(yīng)性強(qiáng)于傳統(tǒng)光學(xué)方案。
模塊化部署方案
提供即插即用型視覺(jué)模組與開(kāi)放API接口,支持快速集成到現(xiàn)有設(shè)備,改造周期控制在3-7個(gè)工作日。
全流程數(shù)據(jù)閉環(huán)
視覺(jué)系統(tǒng)與MES/SCADA系統(tǒng)深度對(duì)接,實(shí)現(xiàn)缺陷特征追溯與工藝參數(shù)優(yōu)化,為持續(xù)改進(jìn)提供數(shù)據(jù)支撐。
ROI可量化驗(yàn)證
典型應(yīng)用場(chǎng)景下,設(shè)備綜合利用率提升25%-40%,質(zhì)量成本降低30%-50%,投資回報(bào)周期普遍在6-12個(gè)月內(nèi)。
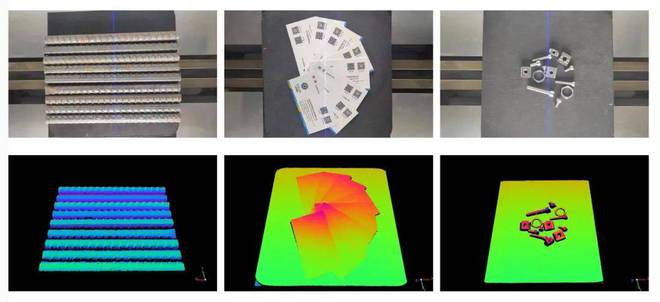
技術(shù)選型建議
對(duì)于中小型集成商,建議優(yōu)先考慮以下技術(shù)參數(shù):
點(diǎn)云分辨率:≥0.05mm@500mm
掃描幀率:≥15fps(動(dòng)態(tài)場(chǎng)景)
防護(hù)等級(jí):IP65級(jí)工業(yè)防護(hù)
通訊協(xié)議:支持Profinet/EtherCAT等工業(yè)總線
當(dāng)前3D視覺(jué)技術(shù)已突破傳統(tǒng)成本壁壘,單站解決方案成本較三年前下降60%,真正具備規(guī);瘧(yīng)用條件。對(duì)于尋求差異化競(jìng)爭(zhēng)力的設(shè)備商而言,融合3D視覺(jué)的智能裝備已成為打開(kāi)中高端市場(chǎng)的技術(shù)通行證。